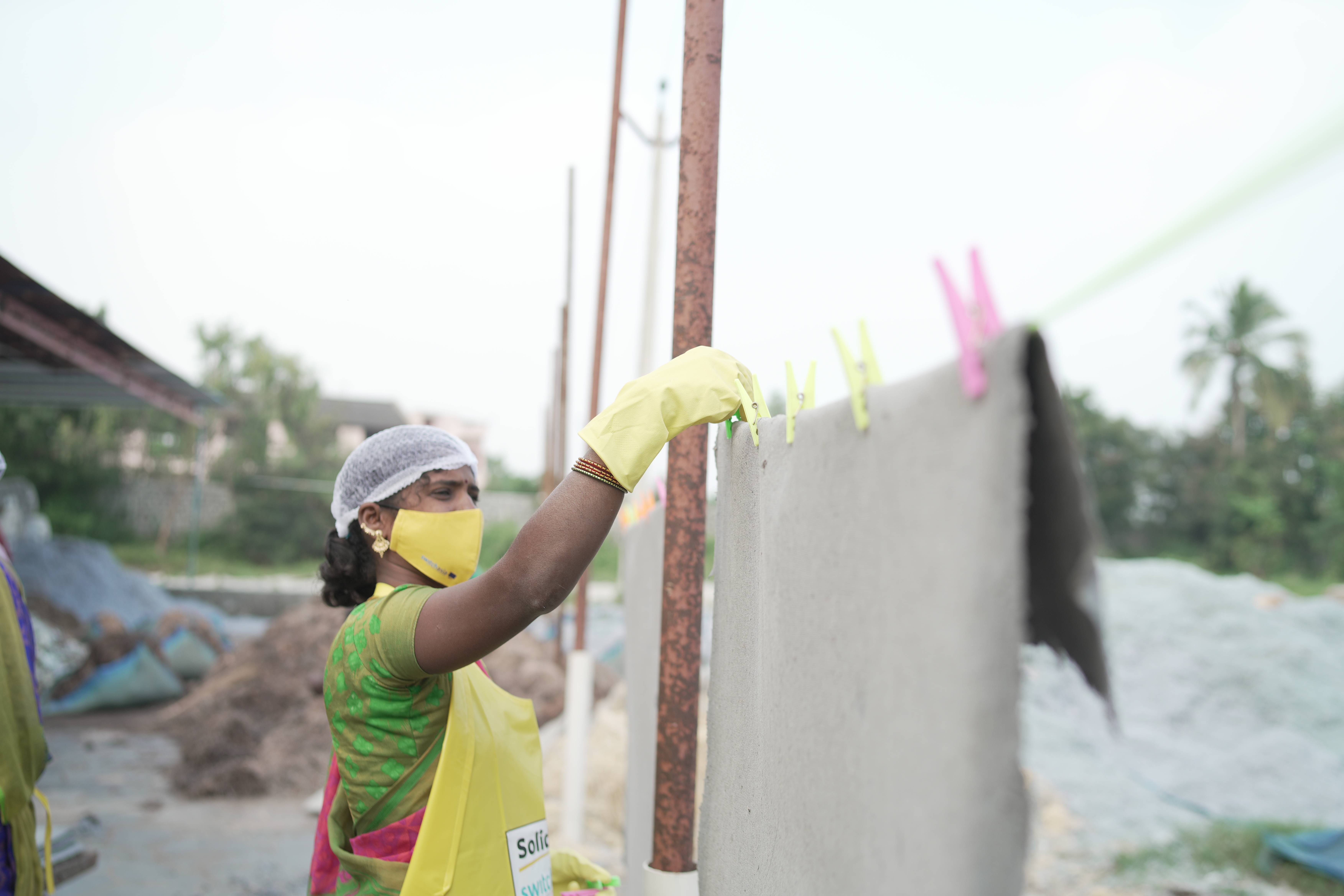
Under the EU–SWITCH Asia Project, Solidaridad and partners are using the circularity approach to implement innovative low-cost solutions to address the solid waste-management issue in Tamil Nadu’s leather clusters.
With nearly 750 tanneries, Tamil Nadu boasts of one of the largest leather clusters in India, contributing to 60 per cent of the country’s tanning capacity and 50 per cent of the total leather exports. A highly water-intensive process, the sheer volume of leather processing operations unfortunately results in a massive solid waste management and disposal issue. The clusters in the state generate a total of 550 tonnes of solid waste every day – in the form of trimmings, shavings, hair, fleshings, buffing dust, sludge salt and more (Solid Waste Baseline Survey, 2022). Not only does this waste dumped at landfills cause severe environmental pollution – air, water and soil – it also leaves behind a significant carbon footprint. Further, with these landfills exhausting their capacity and the Tamil Nadu Pollution Control Board not granting permissions for new sites, tanners incur significant expenses to transport the waste to secure landfill sites. There is an urgent need to devise sustainable solutions for the management and disposal of waste generated by the tanneries in Tamil Nadu’s leather clusters.
Promoting circularity through clean technologies
Launched in 2022, the ‘Promoting Circularity in the Tamil Nadu Leather Clusters for Solid Waste Management’ project is applying circular and sustainable solutions to address the problem of inadequate waste management at Tamil Nadu’s four leather clusters – Ambur, Pallavaram, Ranipet and Vaniyambadi. The project is directly working with 100 tanneries and 1,000 workers in the clusters. Seen as a whole, the project’s solutions are indirectly benefiting 500 small and medium enterprises (SMEs) and 40,000 workers. Funded by the European Union under its SWITCH-Asia programme and implemented by Solidaridad in partnership with the Politecnico Internazionale per lo Sviluppo Industriale ed Economico (PISIE), Indian Finished Leather Manufacturers and Exporters Association (IFLMEA), Council for Leather Exports (CLE) and Tata International Limited (TIL), through a number of circular and eco-friendly measures, this initiative is improving the solid waste-management and water-use efficiencies of the tanneries. These include:
Conversion of chrome shavings into Eco-Particle Boards (EPBs): The manufacturing of EPBs from chrome shavings constitutes the crux of the project’s ‘waste to value’ approach towards treating and processing leather waste. The EPBs possess high tensile strength and flexibility, and also a high tearing strength. More importantly, they have successfully passed the EU’s REACH (Regulation on the registration, evaluation, authorisation and restriction of chemicals) standards. These EPBs have been used to produce several high-quality fashion products such as ladies’ hand bags, tote bags, laptop bags, jewellery boxes, clutches, among other items. In keeping with our aim of establishing a strong business case for the intervention, a pilot-demonstration unit (PDU) to manufacture EPBs is being developed at Ranipet in collaboration with Sowcar Boards and South Indian Leather Boards Manufacturer Association (SILBMA). Once fully operational, the unit is expected to generate significant employment, especially for women. Another PDU(for making value-added products with EPBs) has already been established with a women entrepreneur at the cluster in Chennai.
Conversion of tannery sludge into paver blocks and bio-char: An environmentally friendly intervention, the conversion of large amounts of lime sludge into paver blocks contributes to increasing the waste-management efficiency of the leather sector, reducing dependence on landfill sites for waste disposal. These paver blocks have been proven to meet the necessary environmental standards and possess high compressive strength. Successful pilot demonstrations have been carried out across 15,000 sq. ft. in the Pallavaram tannery cluster at two locations – premises of the Pallavaram Tanners Industrial Effluent Treatment (PTIET) Company Limited and the Alina Shoe Company. Sludge can also be transformed into biochar, an eco-friendly carbonaceous byproduct that can be added to the soil to improve its quality, via the process of pyrolysis that involves the heating of organic materials in the absence of oxygen. Trials are underway, and a cutting-edge pyrolysis machine has been installed at PTIET, Chennai, to study the process and analyse its outcomes.
Reuse of accumulated salt: Instead of using fresh salt, the salt recovered (as much as 40,000 kg, according to estimates) through the zero liquid discharge (ZLD) process (a technology that prevents the discharge of industrial wastewater) is being used for bulk trials of curing and pickling of the leather.
Mr Veerapandian, the proprietor of Sree Venkateswara Leathers which deals in raw hides and skin supplies, says, the ZLD-recovered salt we are receiving from Ranitec [facilitated by Solidaridad] is really helping us efficiently and effectively cure raw hides and skins (…) We would be happy to employ a larger quantity [of this salt] for regular use.
Currently, a process to use the different kinds of salts from the four clusters is being implemented at the PDU unit (with a rotary kiln) in Ranitec. The process of standardization of scientific parameters will be ensured along with the installation of pilot well before upscaling the operations.
Conversion of fleshings into tallow, bio-manure, biogas and aquatic feed: The project is working withindustry experts on exploring the potential of integrating leather fleshings with municipal waste to increase biogas production through the process of anaerobic digestion. Limed fleshings can be dewatered and treated to make aquaculture feed as well. Another sustainable solution involves the utilisation of dewatered fleshings to make bio-compost – 10 kg of fleshings can be used to make approximately 5 kg of bio-compost.
Enzyme-based dehairing: The use of lime and sodium sulphide in the dehairing process is considered economical, but there are significant hazards involved, particularly due to the release of hydrogen sulphide emissions that can affect workers’ health and corrode machinery. The project is therefore working with tanneries to shift to enzyme-based dehairing processes, which are equally cost-effective but remove the occupational risk associated with the other process. Further enzymatic trials are being conducted in the Ranipet cluster, where a polypropylene drum has been installed at M/s PRC Leathers to conduct demonstrations and training.
Process-based optimisations for pollution reduction and water conservation: The installation of solenoid valves in the cluster tanneries has reduced freshwater consumption up to 50 per cent, helping save millions of litres of water in the cluster every year. The smart water saving system (SWaSS), a water-optimisation technology for medium and large tanneries that has been installed in Chennai and Ambur, has similarly reduced freshwater consumption by 30-35 per cent, while also improving the consistency in quality of products. The latest addition to this list of process-based optimisation is the installation of a waterless fleshing roller in a tannery at Vaniyambadi. This affordable Make in India machine aims at 100 per cent conservation of water used in fleshing machines, potentially making it a viable proposition for tanneries in India and abroad.
Desalting machines remove excess salt from hides/skins, thereby reducing salinity at the source. Solidaridad has extensively employed these machines (of different sizes) and upscaled their operations in the three clusters of Ranipet, Ambur and Vaniyambadi. These machines have resulted in 30-33 per cent at-source reduction in the levels of total dissolved solids (TDS) in effluent waste.
Through this SWITCH-Asia project, Solidaridad’s team is doing a fantastic job in bridging the gap. Their innovative initiatives are helping us tackle the solid waste generated in our industry, says Mohamed Jahan, Secretary, IFLMEA.
Capacity-building of workers
While incubating and implementing innovative solutions to tackle waste management at the tanneries, 1,000 workers are simultaneously receiving training on circular practices, eco-friendly tanning solutions and occupational health and safety (OHS). The sessions on water optimisation and eco-friendly tanning practices feature demonstrations of equipment such as desalting machine, SWaSS, waterless fleshing roller, providing a clear understanding of their functioning, utility and benefits over conventional machines.
The OHS lessons focus on different aspects of workplace safety and workers’ well-being: risk assessment, fire safety, safe handling of hydrogen sulphide gas and volatile organic compounds, proper handling/storing of chemicals, safety in machinery operations and electrical installations, first aid, among other aspects. Demonstrations on the appropriate use of personal protective equipment (PPE) are also provided, followed by distribution of these kits among the workers. These proactive measures have led to an increase in capacity and improvement of working conditions among 655 workers in the four leather clusters till December 2023.
Establishing market linkages
With its ‘waste-to-value’ principle, the project aims to support leather workers and entrepreneurs access national and international markets. It is working towards this goal through various initiatives. For instance, products made out of the waste from the tanneries have been showcased at multiple fairs, exhibitions and shows – Asia’s largest leather fashion show (organised by IFLMEA) in 2023 and 2024, the International Leather Fair in 2023, the Leather Accessories Footwear Conclave and Awards of North India (LAFCAN) in 2023, and Aadi Thiruvizha in 2023. This has, in turn, enabled local leather entrepreneurs, artisans and craftspeople to explore and establish market linkages to ensure a bigger market for their products.
Sher Banu, who founded Libua Leathers in 2023 with the support from this project, says: I am thankful for the support provided to women in establishing businesses. [Libua Leathers employs 15 people, 10 of them are women.] Personally, I have been provided high-quality equipment and machines that have helped me immensely. Furthermore, the production samples we designed out of EPBs were showcased at an international leather fashion show, and this has provided us an opportunity to reach out to a bigger market (…) Market linkages are a boon for women entrepreneurs like me.
Alignment with mandates, goals and policies
The multi-dimensional, circular, waste-to-value approach employed by the project therefore aligns with Tamil Nadu’s effort to transition to a resource-efficient and circular economy model. In the process, it also fulfils several Sustainable Development Goals (SDGs): SDG 5 (Gender equality); SDG 6 (Clean water and sanitation); SDG 8 (Decent work and economic growth); SDG 9 (Industry, innovation and infrastructure); SDG 11 (Sustainable cities and communities); SDG 12 (Responsible consumption and production) and SDG 13 (Climate action). In addition, the project also realises the vision of two key aspects of the European Green Deal: eliminating pollution and sustainable product policy.
Building a sustainable future, hand-in-hand
Our interventions are not only industry-centric but also people-centric. Safer work practices and a better ecological balance is our mantra, says Suril Panneerselvam, Programme Manager-Leather, Solidaridad India.
By December 2023, the interventions of the “Promoting Circularity in the Tamil Nadu Leather Clusters for Solid Waste Management” have resulted in:
- The reuse and repurposing of around 100 tonnes of solid waste
- Water savings of nearly 1.5 million litres
- Reducing greenhouse gas emissions to the tune of 35tCO2 eq/year (in 2023)
Still, much needs to be done. Solidaridad has initiated discussion with Tata International Limited, the technical partner in the project – followed by a knowledge expedition for stakeholders from Tamil Nadu’s leather clusters to TIL’s leather facility in Dewas, Madhya Pradesh – in order to implement sustainable practices in the leather clusters. In continuation to the discussion, samples have been received and are being tested at cluster levels for establishing a Project Demonstration Unit (PDU) on a PPP mode in the near future.
The project intends to implement more gender-centric interventions to pave the way for the creation of self-reliant communities. There are also plans to harness the potential of carbon capture and mitigation to a greater extent than ever before. By June 2025, the project aims to utilise 1,040,000 kg of solid waste (resulting in carbon mitigation of 600tCO2eq/yr) and to reduce the consumption of fresh groundwater by 2 million litres per year with its implementation of circular models in association with public and private stakeholders. A plan to train nearly 500 artisans (with a minimum 50 per cent of women, inclusive of persons with disabilities) before the end of the project, is also currently in the works.
Photo credits: SWITCH-Asia Promoting Circularity in the Tamil Nadu Leather Clusters for Solid Waste Management project